Soldering methods with standard solder do work reliably long term but take extra effort to implement.
Solders tailored for this type of application make soldering easier.
Acid fluxes tailored for difficult materials are available. These are totally unsuited to PCB level soldering but are acceptable for wire termination such as this as long as instructions are properly followed. (This requirement is not unique to acid flux - anything can cause problems if instructions are not properly followed).
Crimp methods are common and work "well enough" in many cases. Crimps on even standard wiring in demanding environments can be extremely unreliable longer term if not carried out correctly. In this case "correctly" may be specified by a manufacturer for Nichrome use with a given connector but, if not, then enthusiastic "works well for me" advice which is not based on long representative experience or manufacturers advice may led to longer term disasters.
Be careful with crimping: Crimp connection is a widely used solution for wiring termination and in many cases works well. In demanding situations it can often produce poor reliability.
I at one stage did some work looking at fault sources for people who had a reasonably large number of electronic systems installed in a number of taxi fleets. Equipment included taxi meters, printers, EFTPOS readers, GPS, roof lights and more. A wide range of installers who were considered to be competent had done installations over some years using standard crimping tools and standard wire and cable types. In installations where there were problems a significant proportion had connection issues which could be remedied by rebuilding crimped joints. Which crimped joint was the bad one in any given case added to the fun. Soldering joints which had been crimped cured such connection problems and solder joints were not a significant trouble cause.
The above was with copper wires, not Nichrome.
Nichrome can be expected to be more difficult to manage well.
Nichrome termination:
I've used scrape, wrap, solder as in second method below, with good-enough success. Not always pretty. Clamping mechanically is often used.
(1) All State 430 silver-containing solder.
The advice below actually sounds like it may work.
The magic may be in the silver and the flux. So, other solders may work.
Their method involves:
Silver-containing solder
plus Duzall flux (highly corrosive acid based)
to tin the wire out of circuit
allowing it to then be soldered in circuit with 'normal' solder.
Note that Duzall is extremely corrosive and will happily eat anything electronic that comes in contact with it. This method sounds potentially workable but careful cleaning after tinning is essential.
Discussion group recommendation of Dynagrip #430 kit from All-State
They say:
- Dynagrip #430 kit from All-State includes 4' of silver bearing solder and a small dropper bottle of Duzall liquid flux
Another company that makes a small kit is J W Harris out of Mason, Ohio
They even make kits to solder aluminum.
These kits can be purchased at nearly any welding supply store. They also work good for soldering the ends on SS motorcycle cables.
Do not try to silver solder the nichrome wire directly into the circuit--just tin it with the silver solder and then regular solder works FB to attach it to tie points or whatever.
ESAB selling All State 430 solder
Their aim is stainless steel soldering.
They say:
Cadmium free, low temperature, food grade, solder for high strength on stainless steels, and dissimilar metals. Deposits closely match stainless, and stay bright after prolonged service. Use with All-State Duzall flux or All-state 430 flux.
Extra Info
Recommended applications: stainless steel food handling equipment, refrigeration and air conditioning equipment, instrument manufacturing, electrical work where higher conductivity is required and other applications where strength and ductility must be higher than common solders offer.
Procedure:
Degrease joint area.
Place All-State Duzall liquid flux on joint area.
Use any heat source that will produce 430°F (221°C)in the base metal.
If torch is used, heat indirectly and avoid burning flux.
Apply solder when flux starts to bubble.
Allow to cool slowly.
Remove flux residue with hot water.
When soldering stainless steel types 430, 316, 321 or 347, use All-State No. 430 Acid Flux.
(2) Scrape, wrap solder:
MakerBot method - wrap in solderable wire & solder.
Note that the method involves several steps, all of which will help success (probably :-) ). I'd add a cleaning step at the start. See their page for pictures.
Strip two wires.
Clean NiCr by abrasion.
Overlap wires and wrap with bare 40 gauge copper.
Bend ends of wires being joined back over join.
[Plier mild crimp here probably useful]
Wrap again with 40 gauge wire.
[Crimp again?]
Solder
Their image, before final soldering: Crimping along the way and tighter wrapping could produce a reasonably good looking result.
Photo - BEFORE final soldering
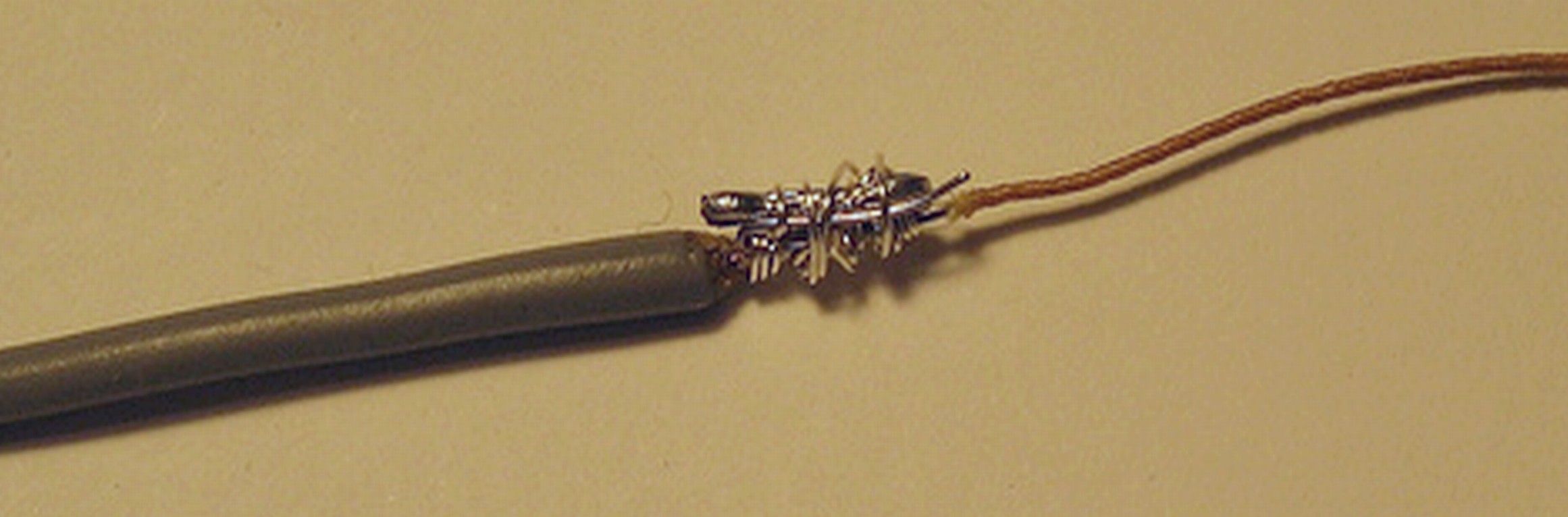
This could be reasonably OK in appearance with due experience.
It relies on NiCr either actually being soldered to some extent OR being trapped mechanically inside a solid soldered copper-copper shroud. In the latter case it may work well but YMMV`. Take due care.
` - YMMV - Your Mileage May Vary - If you've never met it substitute "Caveat Emptor" :-).