Ah, ceramic input capacitor strikes again.
...Most likely. I'll explain that a bit more, later. First, the capacitor itself:
The AVX KGM15CR51C226MT does not have a datasheet (AVX provide sadly little data on their ceramic capacitors), but we can look up a comparable 22uF 16V 0603 X5R part, such as the Samsung CL10A226MO7JZN, which does:
https://weblib.samsungsem.com/mlcc/mlcc-ec.do?partNumber=CL10A226MO7JZN
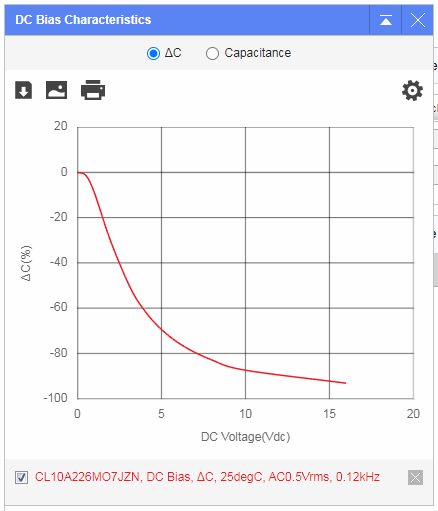
You appear to be applying 24V which is unsafe for the 16V part anyway, but the dielectric and construction will not differ significantly from this part and we can assume there's a flea-fart's capacitance left at this voltage.
For a 10A class converter, I would expect more like 4-8 x 1206 or even 1210 chips, or a couple 0805s plus a polymer, and in either case an electrolytic would be welcome to absorb further ripple current plus dampen any input-circuit resonances.
Because type 2 ceramic capacitance depends on voltage, it's neither economical nor practical to select the largest possible value in a given voltage rating and chip size. Indeed, Digikey presently shows only three items of comparable rating, out of nearly a million items in the category; you selected quite the rare part.
More typical would be 4.7 to 22uF, 25 to 50V, 1206 or 1210, and such values will be available in X7R, which tends to have a flatter curve, also in terms of temperature (105°C rated).
As for function, SMPS controls typically assume a low and stable input impedance, or a stable input voltage. Clearly, neither of those are true here..!
There are two significant consequences for an under-damped input filter:
Hot-plugging; inrush surge. This is a very common cause of failure among SMPS questions here (hence my comment).
Even if the capacitor were linear, hot-plugging a voltage source to a lossless series LC circuit generates a peak voltage twice the input. Since C depends on V, as V rises, C decreases, dV/dt accelerates, V rises even further, C decreases even further... The resulting peak voltage can be five times the input, easily.
Oscillation due to the converter's negative input impedance.
That is, current draw decreases as voltage rises -- it conserves power more or less, so this is simply a natural consequence: negative (incremental) resistance. Depending on control type, this can manifest at frequencies as high as Fsw, or disappears above some fraction thereof (at frequencies where the control loop can't act fast enough to maintain constant input power), but in any case applies from DC up to some at least modest AC frequency which can include the input filter resonant frequency. Those frequencies overlap, the negative resistance exceeds loss resistance at that frequency, and off she sings.
So, simply dampening that with a bulk capacitor of nominal ESR, such as an electrolytic capacitor, keeps the regulator input happy. 100uF in polymer or electrolytic would be welcome, with more like 1000uF electrolytic being typical.
While it's true this may not be the explanation for the totality of observed behavior, including the clicking or bouncing or restarting, solving this is a prerequisite for further analysis.
By the way, did you catch this juicy little bit? A closer look...
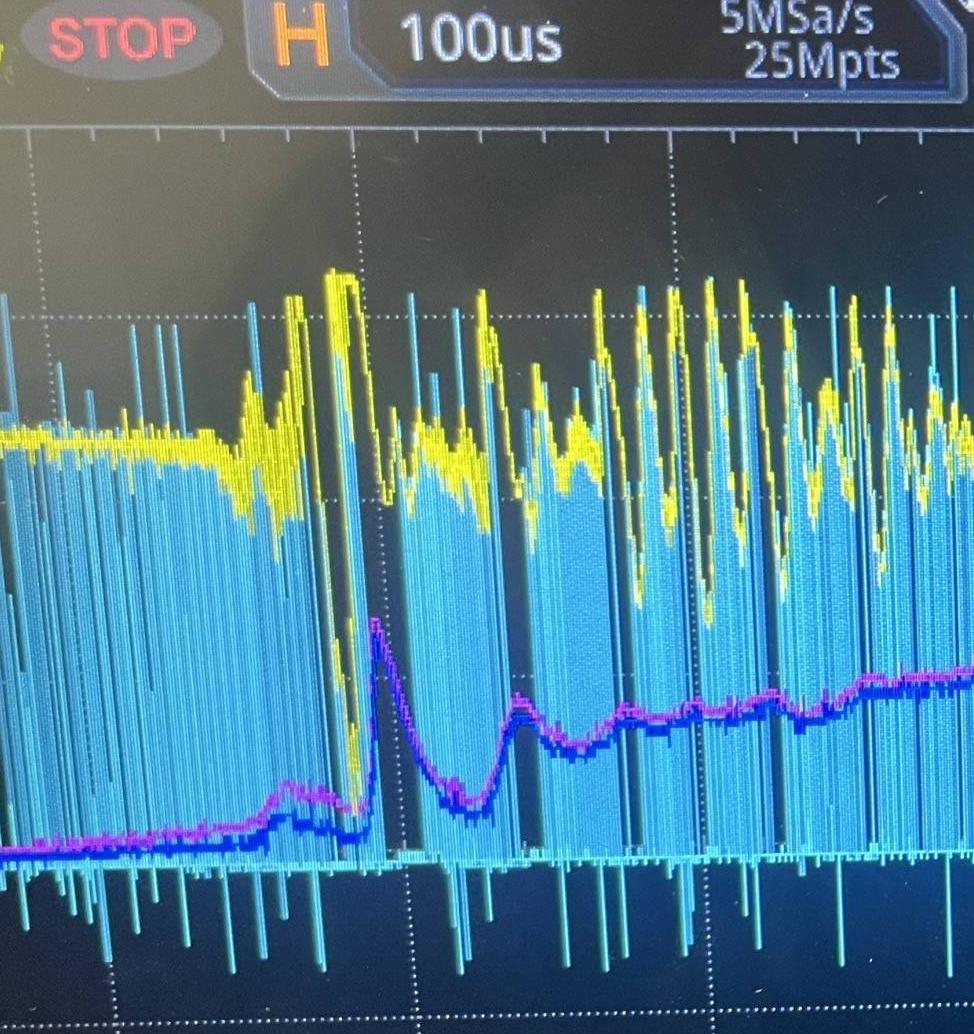
That peak looks suspiciously flat-topped, and if I'm not mistaken, that's a peak around 32V. On a device rated merely 28V... methinks you've observed avalanche breakdown, and are damn lucky the thing didn't fail shorted already!
24V is very tight to be operating a 28V converter at, anyway; I would advise keeping it under 20V, and using a TVS and electrolytic at the input, to dampen overshoot and ringing, and clamp overshoot to within the regulator's ratings. Else, get a higher-voltage rated regulator. Headroom around 40% (rated vs. nominal-max operating voltage) is recommended, give or take application.
Further reading: recently I simulated the transient, by itself as a startup (inrush) surge (not including the converter here), and collected a few related questions on the phenomena, in another answer:
https://electronics.stackexchange.com/a/713473/311631