How to get the most out of a potentiometer?
In many precision, low-noise designs, it's a bad idea to start with to even have the signal routed through the front panel. So, at the very least, the control element should merely produce a voltage signal that governs a voltage-controlled amplifier/attenuator. With a potentiometric source, you can buffer and low-pass-filter the control signal, so that wiper dropout effects are minimized.
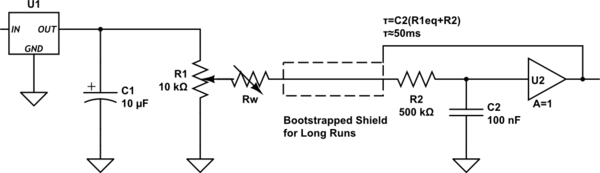
simulate this circuit – Schematic created using CircuitLab
Here, a voltage reference feeds the potentiometer. The variable wiper resistance is modeled by Rw, which can vary by 9 orders of magnitude, but is mostly "low" and on the order of an Ohm. R2 keeps the time constant above 50ms. Since R2>>R1, R1's influence is small. C2 forms a low pass filter with R1+R2, but also acts as a hold capacitor. U2 is an op-amp set up in non-inverting mode, so that its input has a very high impedance. The output of U2 goes to a voltage-controlled amplifier.
C2 should be a low-leakage type with NP0 or plastic dielectric, and U2 should have a FET or CMOS input stage. So, don't use 741 for U2 with expectation that it would work all that great - although it will still work better than the naked potentiometer would.
If the wire from R1 to the circuit is long, you might need a bootstrapped shield. Some experimentation is necessary to ensure stability of the circuit then, though, as the shield-to-signal capacitance adds positive feedback to the system.
That already gives you a much better performing circuit than using a potentiometer directly on the signal. Even with a fairily short 50ms time constant, you can get rid of crackle even on the most ridiculously dirty potentiometers. You can always trade off response time for insensitivity to crackle.
Routing audio to front panels is usually an EMI nightmare and it's often not cheap at all to do it properly.
Voltage Controlled Gain
A good bang-for-the-buck voltage-controlled gain element can be made by using a photoresistor illuminated by a LED. Photoresistors, if you select them, can have very low voltage coefficient of resistance and thus very low distortion, certainly beating most simple multiplier circuits by an order of magnitude or more. They are available as self-contained units, known as Vactrols, from Excelitas. They need to be applied with some care, as you don't want to exceed about 100mV across the photoresistor, but otherwise they are wonderfully powerful devices for about $5 each.
There are decent integrated voltage-controlled amplifiers, such as the last-time-buy (sadly) SSM2018, or newer AD8338, THAT2181, etc.
How about rolling contact?
If you still have a mechanical mouse, open it up. Take the ball out and look at the rollers. Invariably they'll be covered with a hardened track of grime. Rolling contact isn't all it's cracked up to be if you can't control the environment quite well. Sliding contacts have a self-cleaning property. Rolling contacts, in a potentiometer, would have the exactly opposite behavior - they'd be self dirtying. That'd be a very bad idea.
Mechanically there's another aspect you seem to forget: rolling contact is wonderful at concentrating the stresses, and requires sufficiently hard surfaces to prevent wear. It's kinda hard to make a low-power resistive sensor where the surface needs to interface with a metal ball/roller while having any sort of useful life expectancy.
If you really don't care about the power of the circuit, you're fee to make the resistive track, C-shaped, out of hardened steel. Feed it a couple of amperes, in pulses, use a sample-and-hold circuit to get the pulse amplitude, and you're set. It'll work as long as you house it in a dust proof enclosure. Note that dust-proof is usually harder than water-proof (!).
TL;DR: The rolling contact would be possibly the worst thing you'd ever wish in a potentiometer wiper.
So, what other options are there?
You can obtain the signal from other sources. They all work by converting shaft angle into a voltage, using a variety of techniques. I present them in no particular order.
Noncontact Potentiometers
Suppose that you start with a basic, C-shaped resistive track of a potentiometer. Choose a large one, so that it's easy to work on. Open it up. Bend the wiper so that it's lifted up from the track, but just ever so slightly. Feed the track with an AC signal, say a 1MHz square wave, with the other end of the track at 0V. The wiper is capacitively coupled to the track, and will pick up a signal whose amplitude is proportional to the position on the track. You will need to tweak it to get rid of the worst parasitic capacitances, but work it will. You can use a FET follower or an op-amp to lower the impedance of the wiper's signal, then use a synchronous demodulator to convert the amplitude back to baseband. It might sound fancy, but for such a simple sensor you can do it on a couple dollars worth of parts, nothing fancy needed at all. You don't need any better than 10% linearity anyway.
Variable Transformers
A very precise, and perhaps an over-the-top source would be a RVDT (a rotary cousin of an LVDT). For a one-off "vanity" project, it'd be a nice choice - these things are virtually indestructible, and with luck you can get them cheaply from surplus. For a volume control, you could make a very simple RVDT conditioner (the circuit is same as for an LVDT).
Variable Capacitors
Another vanity option would be an old, heavy, rotary capacitor. The better ones have a pair of ball bearings. Similar to an RVDT, they have no other contacting parts to wear out. Put the capacitor in a multivibrator circuit, hook up to a voltage-to-frequency converter circuit (LT app notes have plenty of those), and you're set.
Magnetic Sensors
A much lower cost option would be a Hall sensor. Suppose you have a magnet oriented radially on a shaft, and a Hall transducer next to it. As you rotate the shaft, the magnetic flux passing through a properly placed sensor will vary. This is a good source of a control voltage - cheap to implement, too.
Optical Sensors
You can also have an optical sensor: print a V-gap, with X-Y mapped to polar coordinates, on a sheet of transparency foil. Install on the shaft. Put a LED-photodectector pair so that it "sees" through the gap. Condition the photodetector (either a transistor or a diode) with an op-amp.
Another optical option that doesn't need a V-gap would be to have a tilted disc mounted on the end of a shaft, so that it's not quite perpendicular to the shaft's axis. Then use a reflective sensor (LED + photodetector) to obtain a continuous signal proportional to the angle.
Another optical option is to have a multiphase pattern printed on a cylinder on the shaft, and use multiple optical sensors, with their outputs summed, provide the output. The pattern might look as follows:
axial distance
^
| █████████
| ██████
| ███
|0---------360--> angle
As the cylinder turns above the sensors, their outputs get progressively lower. By judiciously tweaking off the number of detectors/stripes, and the detection distance, you can get by with a simple black-and-white pattern. Sometimes that's easier to manufacture than something fancier.
Strain-to-angle Converters
Yet another option, quite sensible if you know how to deal with strain gages, would be to have the shaft interface with a long spiral spring. Slap a 4-gage strain gage bridge somewhere on the spring, with the sensitive axis along the spring's length, and you get a very nice signal proportional to the shaft angle. You'll need to add a bit of friction into the mechanical circuit so that the shaft stays put when you release the knob.
Odds-and-ends
Yet another option, if you want to get funky, would be to have a variable acoustic capacitor. Have the shaft go through a flat toroidal box. It can have a rectangular cross section, of course. Make a radial slot through the inside of the box, and extend a radial pin from the shaft through the radial slot. Attach a paddle that almost fills up the box's cross section to the end of the pin. At the zero point in the box, add a partition and an acoustic transducer. Attach it to an oscillator, and you've got an electro-acoustic angle-to-period converter.
The above are only the things I have tried, with some degree of success, at some point in life. There's almost an infinite supply of other ideas, if you want to have some transduction fun.