I'm designing an impedometer myself and think I can simply explain the basic principle in layman's terms. This answer originated in trying to explain the question (about the 50%) in the asker's first comment to Richman's answer with a simple animated picture I made for this question that explains everything without words):
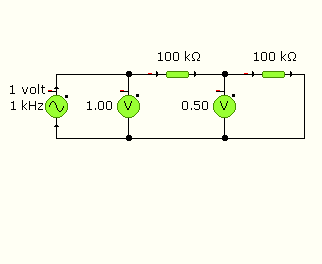
Impedance (Z) is basically just the resistance (R) a component poses to an AC-signal at a specified frequency (Hz), because (unlike a straight-forward DC application) resistance varies under frequency.
So, moving to the animated picture (where the 'slide' without a wave-form is the first image).
You can see a basic voltage divider: 2 equal-value resistors in series, fed by a 1 volt pure sine-wave ac-signal @ 1kHz.
Between the signal-source and the first resistor (red arrow) is a voltmeter (referenced to 0-volt/ground) that displays the voltage that the signal-source gives: 1 volt (=100%). Let's call this the 'reference voltage' (Vref).
Between the first and second resistor (blue arrow) is a second voltmeter (again referenced to 0-volt/ground) that displays the voltage(-drop) between those 2 equal resistors (aka voltage divider): 0.5 volt (=50%). Let's call this the 'test voltage' (Vtest).
Obviously, when the two resistance-values are equal, the voltage divider divides by 2 (aka 50%).
In the second 'slide' you can clearly see the voltage's waveforms (at the red and blue arrow) and how they relate on both halves of the wave (positive and negative).
Using this logic, you could also use a potentiometer or rheostat (displayed in the third 'slide') as a test-resistance (instead of a fixed value resistor). Of course the principle will still hold true.
So say you did not know the value of the second resistor (the one after the blue arrow), you could use a variable resistance as (first) test-resistance and turn it down until you have a 50% voltage drop (Vtest, referenced to the input signal (Vref) that is 100%). Naturally this variable resistance must cover the expected impedance range that you want to measure!
Now if you measure the test-resistor's (first resistor) value with an ohm-meter, you should have found the impedance (resistance) value of the unknown second resistor at specified frequency (and signal-level/voltage).
For audio purposes impedance is usually measured at 1kHz, but there is nothing stopping you from making a graph over a specified frequency range: just change the frequency, change the variable resistance until you have a 50% voltage drop and finally measure that resistance. This is often very useful in measuring speakers (coil reacts a lot more to frequency) for instance.
For your purposes 'slide' 4 comes into play: the second resistance is simply the component/coil/device you want to measure. That's it, again nothing new to learn. Now that was an easy slide right? :)
(A good thing to know/realize is that most manufacturers simply specify the resistance-value of the first resistor that 'loads' the signal to 0/ground at the amp's input.)
Another way to use the same principle (still nothing new to learn :) ), would be to have a fixed-value test-resistor (as first resistor) and calculate the impedance purely based on the voltage after that first resistor (Vtest at the blue arrow).
Simply put: say you have a signal level of 3 volts and your test resistor is 100k and you have a voltage-drop of 1 volt (1 third), then the impedance (value of the unknown second resistance) must be 200k (2 third) at that specific frequency.
Formula: Z=R*(Vref/Vref-Vtest)
Read more about this over here where this (and output impedance) is covered.
Now that the principle is clear, some thoughts about designing your own meter.
When selecting/researching parts, don't forget to look at their power supply requirements (single or dual rail voltage).
You also want to know how 'smart' your meter is going to be (are you ok with using an ohm-meter across two exposed test-pads) and if you want to go analog or use a micro-controller and lcd? And of course you need to know for what ranges in impedance, frequency and signal-level you are designing.
So first you need a (pure) sine-wave generator (do you need the ability to select frequency's and in what range and step-size? What about displaying the test-frequency?).
Next you might want to have a small op-amp (buffering and amplify the sine-wave) and a way to regulate (and monitor?) the output-level. Don't forget you also might want to attenuate the signal-level down to phono/mic levels, up to dbu/dbv, 4.5 volt for active emg guitar-pickup's and up to 6.5 volts for active emg bass-pickups (note that you now have breached the common 5 volt ic ttl barrier).
Then options grow exponentially..
If you want to go the mcu way, that does it's readouts and (spectrum-sweep?) automatically (maybe even display a nice graph), then I think measuring and calculating the voltage is the simplest (versus the probably more accurate resistance-measurement). Hence the resolution of the adc matters! (this is where Richman's answer comes into play.)
However if you specifically want to measure the resistance's value (what can be done with a mcu to.. and might be more accurate, or useful as a simple 'device to be used with your existing ohm-meter', then the comparator (or op-amp connected as comparator) comes into play (as this compares to voltage-levels and gives logical yes/no output).
One nice thing to notice (if you look at the wave-form in the image) is that when handling dbu/dbv like voltage levels you could feed Vref and Vref through a schottky diode (low voltage drop) (making a half-wave rectifier) and use a cheap dc-comparator (especially when using an external existing sine-wave generator). Since even at 100hz, an indication-led will flicker faster than you can see.
Another thing to notice is that a single rail powered, ac-capable quad op-amp has all you need (apart from a signal-source) for a simple device: 1 channel to buffer the signal and 1 channel configured as a comparator (driving a indicating led) comparing: a 50% reference-voltage (same voltage-divider schematic as the first 'slide') buffered by the third channel with the test-voltage buffered by the last channel.
Some thoughts on accuracy: when using a digital pot, the step-size will determine the accuracy greatly, but makes design of a stand-alone meter easier.
When using (analog/optical) switches (to select the range of your test-resistor) keep a keen eye on it's Ron (you preferably want <0.5 ohm) and capacitance, but also it's Roff!! They also need to pass ac or be 'immune' to reverse voltage (within your testing-range).
When using an mcu calibrating the meter (taking account for internal component resistance) is also simpler, which again increases accuracy.
Hope this helps, I'm happy to share some more thoughts or even collaborate. I once saw a single ic (medical) containing digitally controllable pure-sine generator (I believe also a op-amp) and impedance-meter with digital output. That ic together with a mcu would kick-ass. I'll see if I can find it again.