The main criteria in choosing either IGBT or MOSFET are voltage rating, power losses (efficiency of the whole system) and of course the cost of the whole system. Choosing one over other may impact not only losses in the transistors but also the weight and cost of cooling, size of the complete product and also reliability so sometimes e.g. a weight constrain may force you to use MOSFET instead of IGBT.
If you look at this graph, you will see different areas, where each type of switch are typically used:
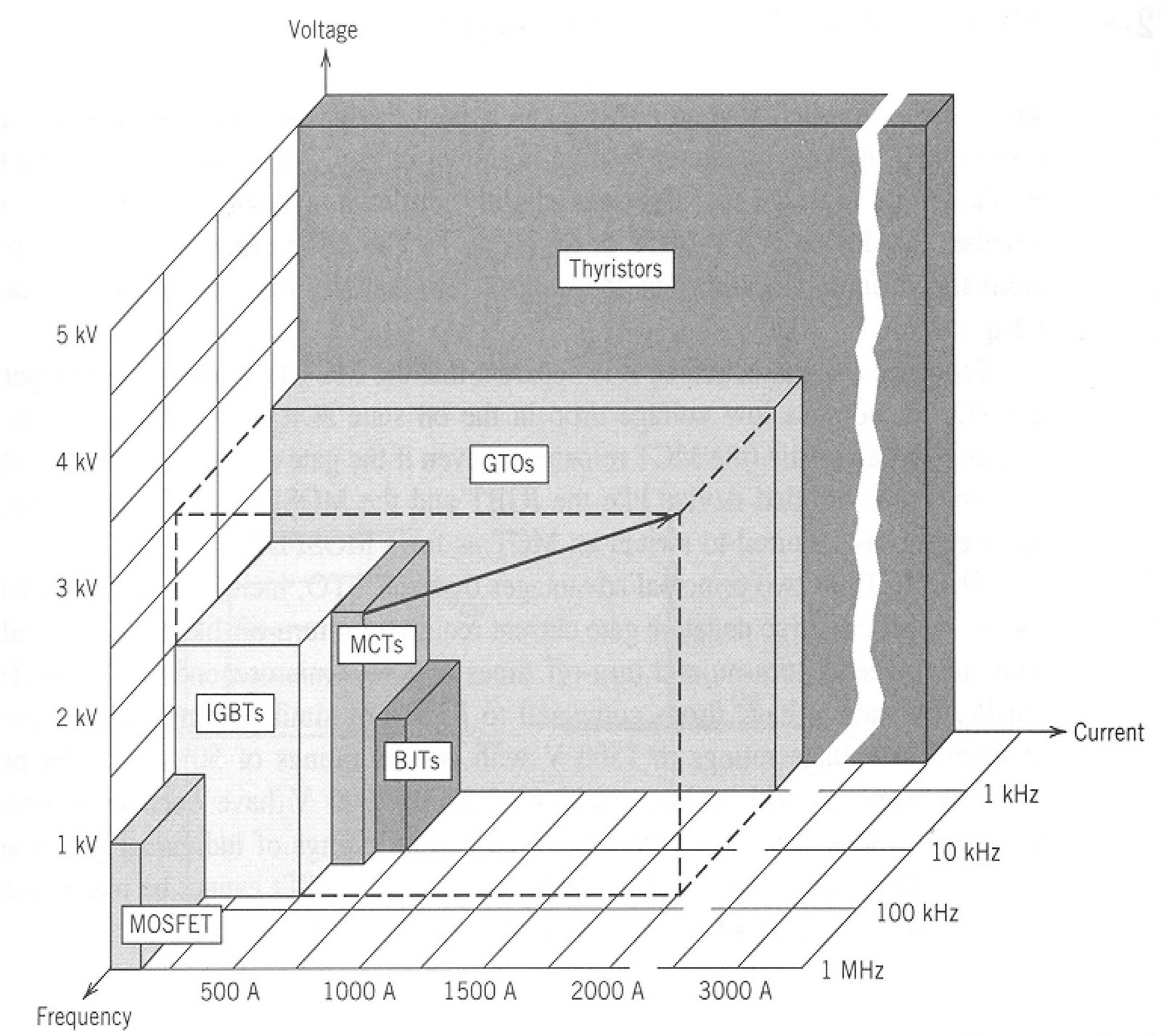
Choosing a particular device type depends on specific application and its requirements.
MOSFETs dominate in high frequency and low current applications because they can switch extremely fast and act as resistance when on.
Fast switching means they are used when the device has to be small as when you increase switching frequency you can reduce the size of passive filters.
The conduction losses are proportional to the square of drain current and therefore you cannot pass huge current through the structure.
They also have limited breakdown voltage and are typically used up to 600V.
IGBTs have higher breakdown voltage and conduction losses are approximately equal to Vf*Ic therefore you can use them in high current applications. They have limited switching speed therefore they are typically used in industrial applications where low switching frequency is not a problem (acoustical noise).